
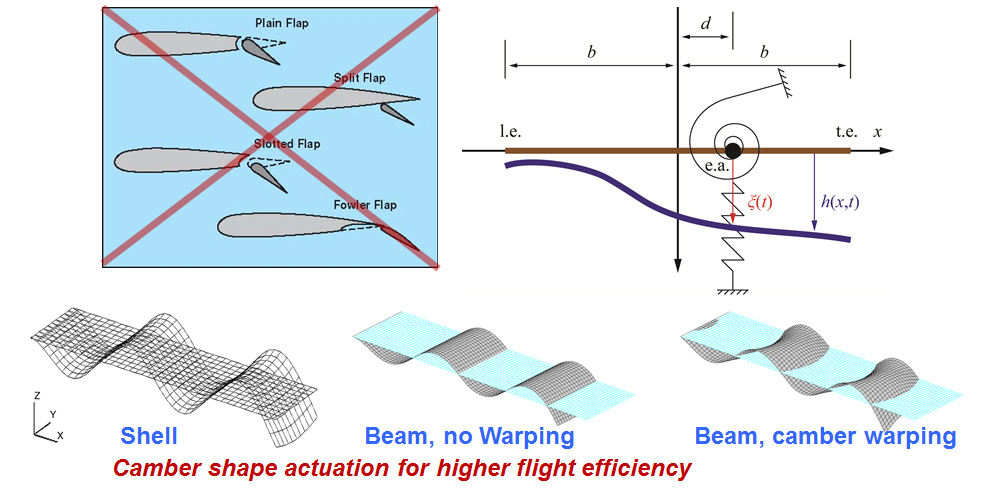
It might take some time until you receive an answerĪnd in some cases you may even receive no answer at all. Page] Suggestions? Corrections? Remarks? e-mail:ĭue to the increasing amount of SPAM mail, I have Shape Reflex and Moment Coefficient Reflex and Lift & Drag Ratio - that's where all the trouble begins. We simply bend the trailingĮdge upward until we achieve the moment coefficient necessary to stabilize ourīut we probably prefer an airplane, which not only flies safe and stable, butĪlso performs with a low sink speed, a high penetration speed and a good L/D Using this trick, the problem seems to be solved. Moment coefficient follows the deflection. Symmetrical airfoil, a flap is deflected smoothly upwards by 5° and 10° - the Shows how C m can be controlled: starting from a In fact, it is possible to adjust the shape near the trailing edge to achieve Part of the camber line has a big influence on C m.

With a reflexed camber line more closely, we find, that the shape of the rear We already know, that the moment coefficient C mĪnd the shape of the camber line are closely connected. Shape Reflex and Moment Coefficient Reflex and Lift & Drag Location of Camber and MomentĬoefficient Dangers everywhere Velocity Distribution and Boundary One digit describing the distance of maximum thickness from the leading edge in tenths of the chord.Airfoil Design for Tailless Airplanes: 3 Airfoils for Tailless Airplanes: Design and Selection Airplane Types and MomentĬoefficient Moment Coefficient and Airfoil.One digit describing the roundness of the leading edge, with 0 being sharp, 6 being the same as the original airfoil, and larger values indicating a more rounded leading edge.
#Camber airfoil code#
The following table presents the various camber-line profile coefficients:įour- and five-digit series airfoils can be modified with a two-digit code preceded by a hyphen in the following sequence: The formula for the shape of a NACA 00xx foil, with "xx" being replaced by the percentage of thickness to chord, is y t = 5 t, Plot of a NACA 0015 foil generated from formula The 15 indicates that the airfoil has a 15% thickness to chord length ratio: it is 15% as thick as it is long.Įquation for a symmetrical 4-digit NACA airfoil The NACA 0015 airfoil is symmetrical, the 00 indicating that it has no camber. įor example, the NACA 2412 airfoil has a maximum camber of 2% located 40% (0.4 chords) from the leading edge with a maximum thickness of 12% of the chord. Last two digits describing maximum thickness of the airfoil as percent of the chord.Second digit describing the distance of maximum camber from the airfoil leading edge in tenths of the chord.First digit describing maximum camber as percentage of the chord.The NACA four-digit wing sections define the profile by: These figures and shapes transmitted the sort of information to engineers that allowed them to select specific airfoils for desired performance characteristics of specific aircraft. Engineers could quickly see the peculiarities of each airfoil shape, and the numerical designator ("NACA 2415," for instance) specified camber lines, maximum thickness, and special nose features. By 1929, Langley had developed this system to the point where the numbering system was complemented by an airfoil cross-section, and the complete catalog of 78 airfoils appeared in the NACA's annual report for 1933. According to the NASA website:ĭuring the late 1920s and into the 1930s, the NACA developed a series of thoroughly tested airfoils and devised a numerical designation for each airfoil - a four digit number that represented the airfoil section's critical geometric properties. NACA initially developed the numbered airfoil system which was further refined by the United States Air Force at Langley Research Center. 2.2 Equation for a cambered 4-digit NACA airfoil.2.1 Equation for a symmetrical 4-digit NACA airfoil.
